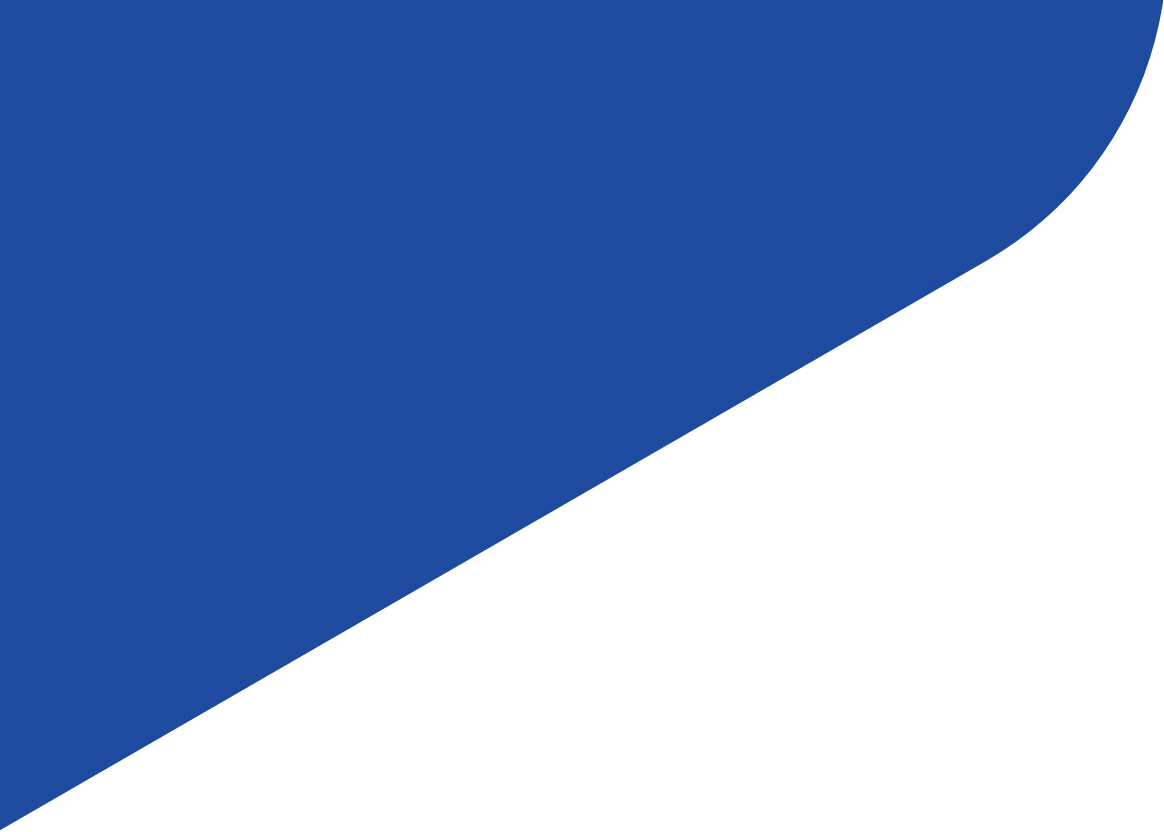
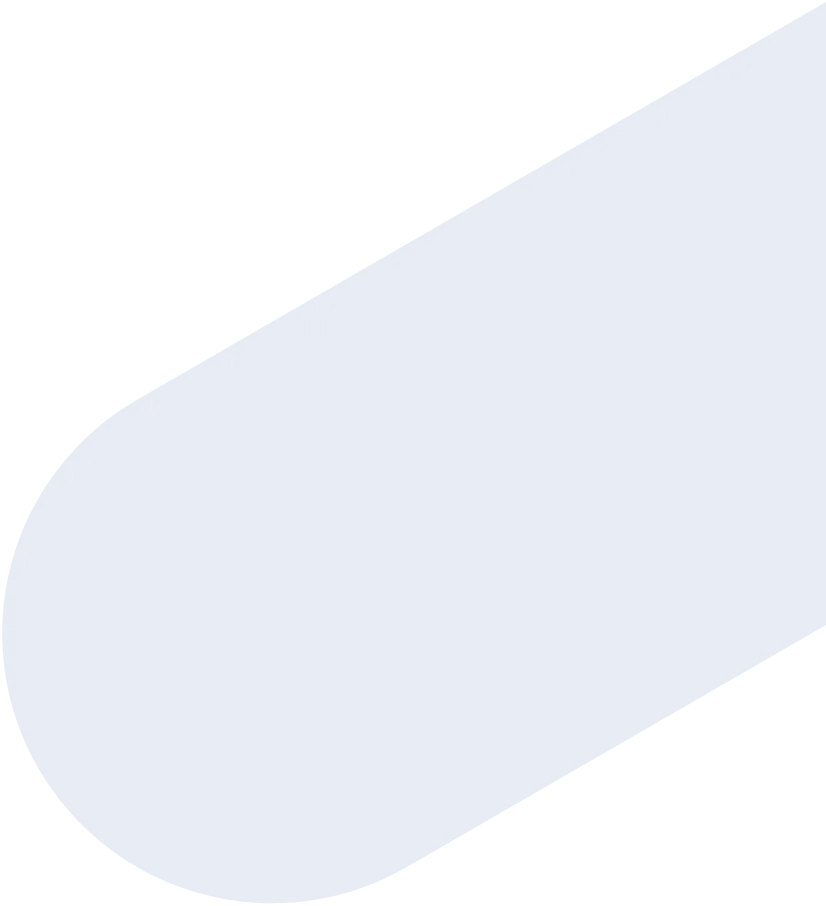
やりたいことに挑み
経験を存分に生かす
それができる企業風土です
コスト競争力を上げる
生産活動に力を注ぐ部署です
多彩なパッケージ製品の製造を担う昭和プロダクツでは、安定的に高品質な製品を製造するのはもちろんのこと、お客様に選ばれるコスト競争力の高い製品づくりに努めています。そうした競争力の向上に比重を置いて活動しているのが製造部です。
部内は4つのチームで構成されています。まず私が担当している、数字を把握・分析して生産活動の状況を調査・管理するチーム、次に新しい商品や材料を広げていくための開発を支援するチーム、設備・機械の開発や製作を管理するチーム、そしてお客様の希望通りの製品ができているかを管理する品質保証チームです。
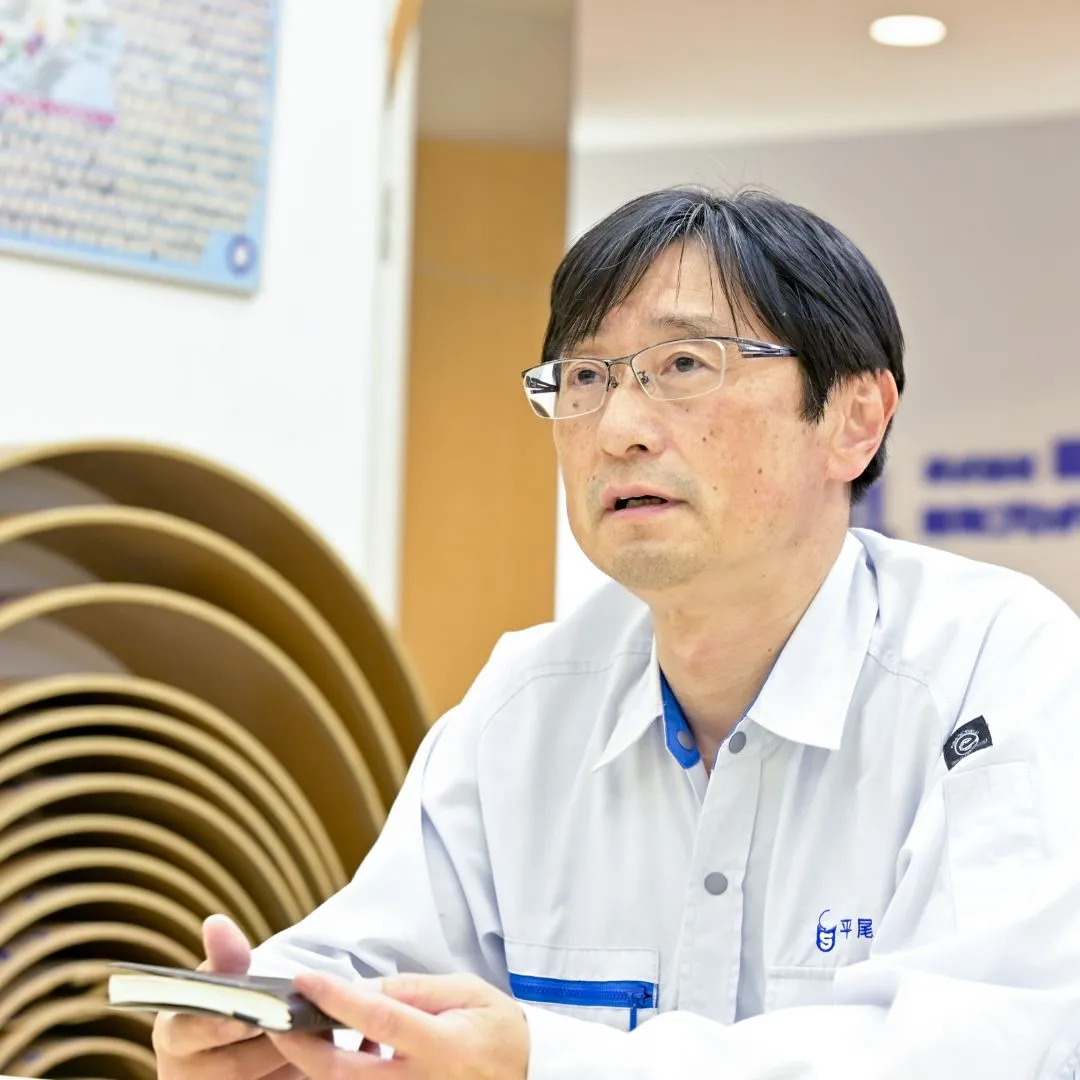
全国に展開する11事業所の
ものづくりの最適化を
担っています
ひとつの製品を作る過程には、さまざまなコストがかかっています。材料費や生産にかかった人件費である労務費、運送費などです。これら製造にあたっての管理可能費の数字を集計し、変化を把握します。国内11の事業所で工場を展開しているため、数字を分析していると、事業所ごとに材料費がどう変わってきているか、前年度に比べて生産性が落ちている事業所があるといった状況が明らかになり、課題が見えてきます。そうした各事業所のものづくりを管理しながら、課題を改善するための活動をサポートするのが私の仕事です。いわば、ものづくりの全体最適化です。
現在はとくにSPIC(Showa Profit Improvement Concept)という、会社の利益を生み出すための活動を全事業所に拡げる活動に注力しています。さらに、事故・災害を起こさないよう安全を守るための活動も担っており、業務の領域はかなり広いです。
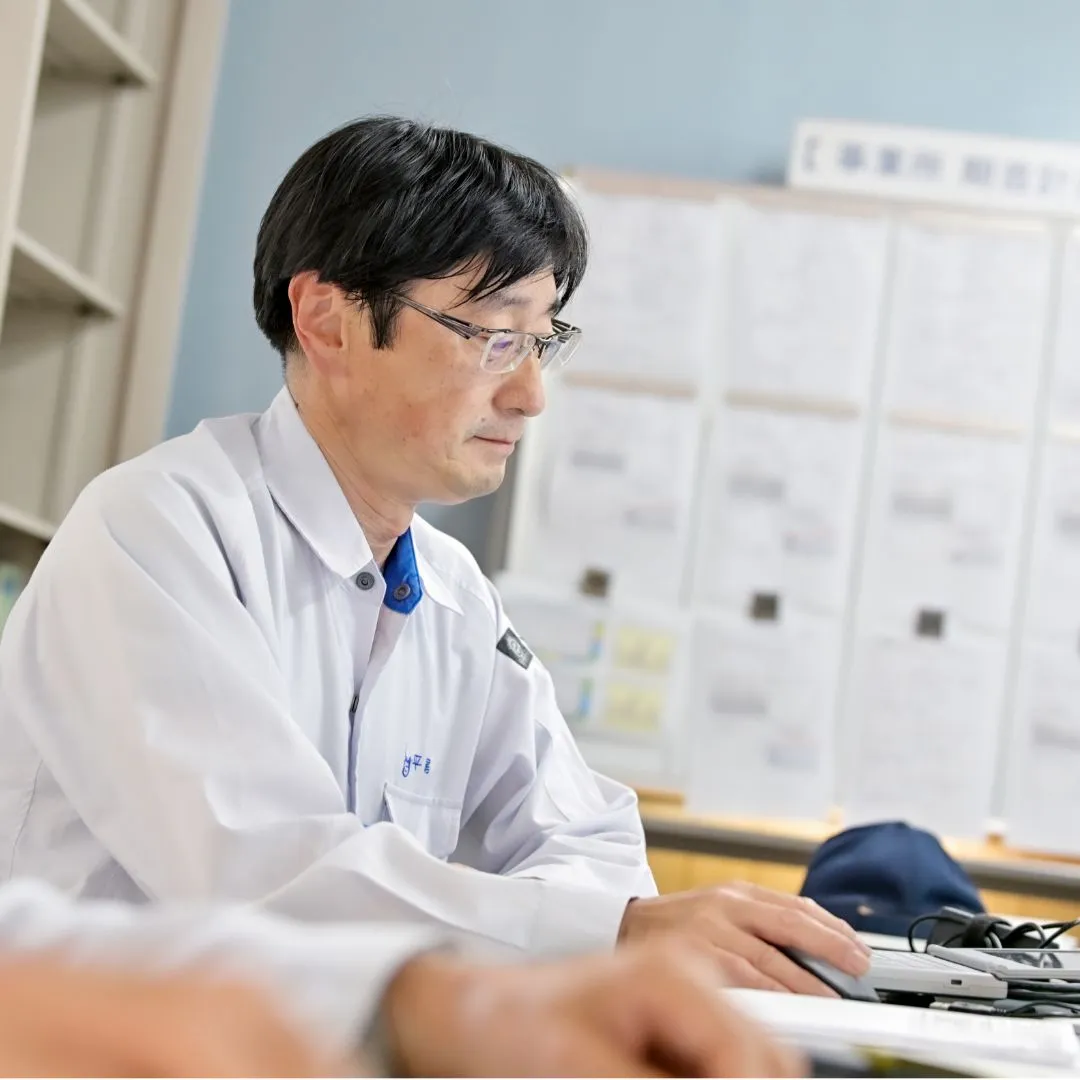
さまざまな部署を経験し、
今がある
経験の大切さを実感します
コストを抑え、品質を担保してものづくりを続けていくために各事業所を回り、問題を抽出して、改善の具体策の提案と実際の取り組みをしています。さまざまな製造現場と一緒に、よりよい生産活動を目指して活動することは簡単ではありませんが、とても手応えがあります。私が心がけているのは、事業所への出張にかかった費用分は必ず改善して帰る、ということ。常にコスト意識を持つようにしています。
入社から随分年月が経ちましたが、経験の大切さをつくづく感じます。試行錯誤の末に新しい価値を生み出すことを心がけていると、その積み重ねが経験になります。
私は理系出身ですが、入社時に営業を希望しました。1年だけ営業を経験し、その後は製造部に移って改善活動に取り組み、次は製造部を離れて事業所で所長などを務め、また製造部に戻ってきました。こうしていろいろな仕事を経験できたからこそ、生産活動の全体が見えるようになったのだと思います。
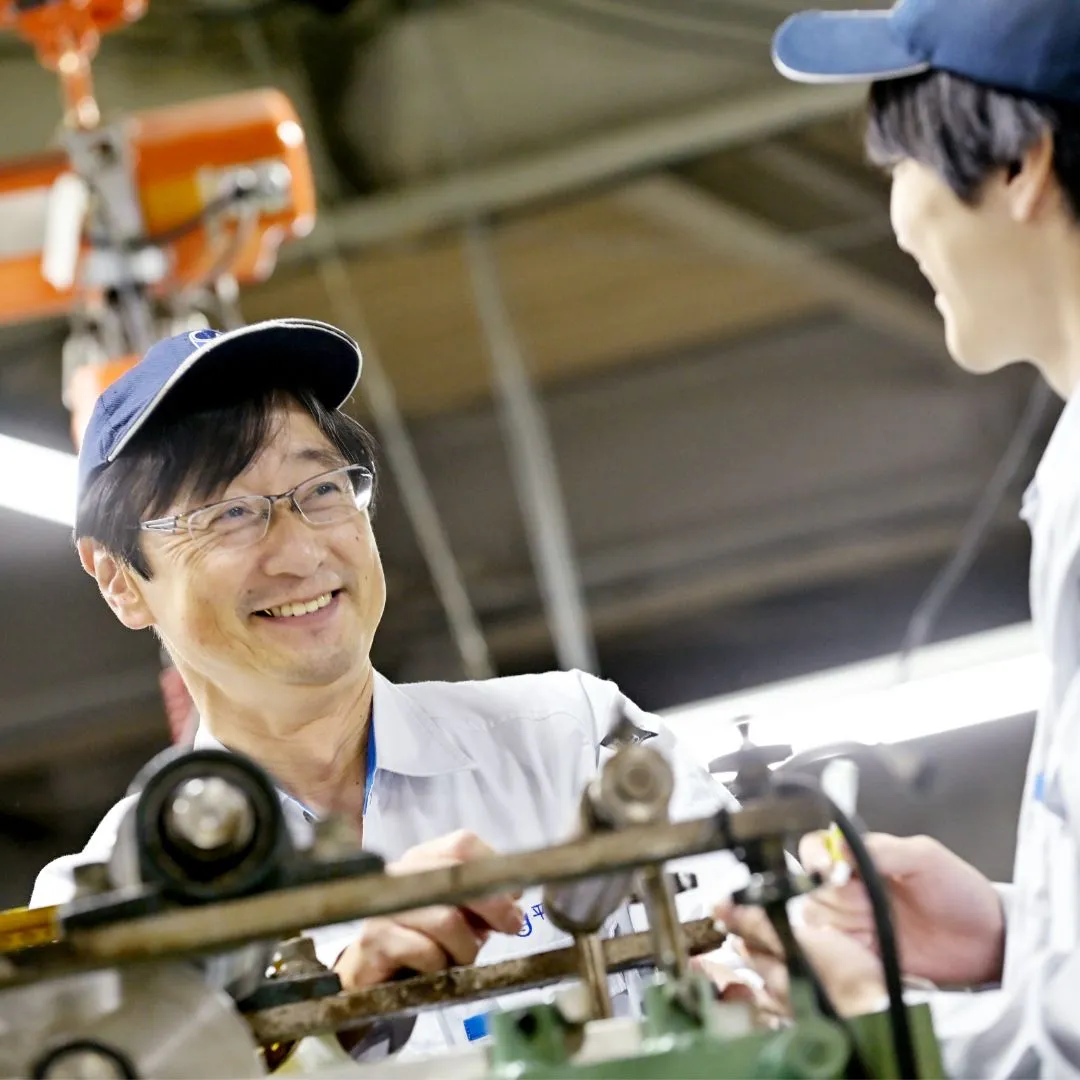
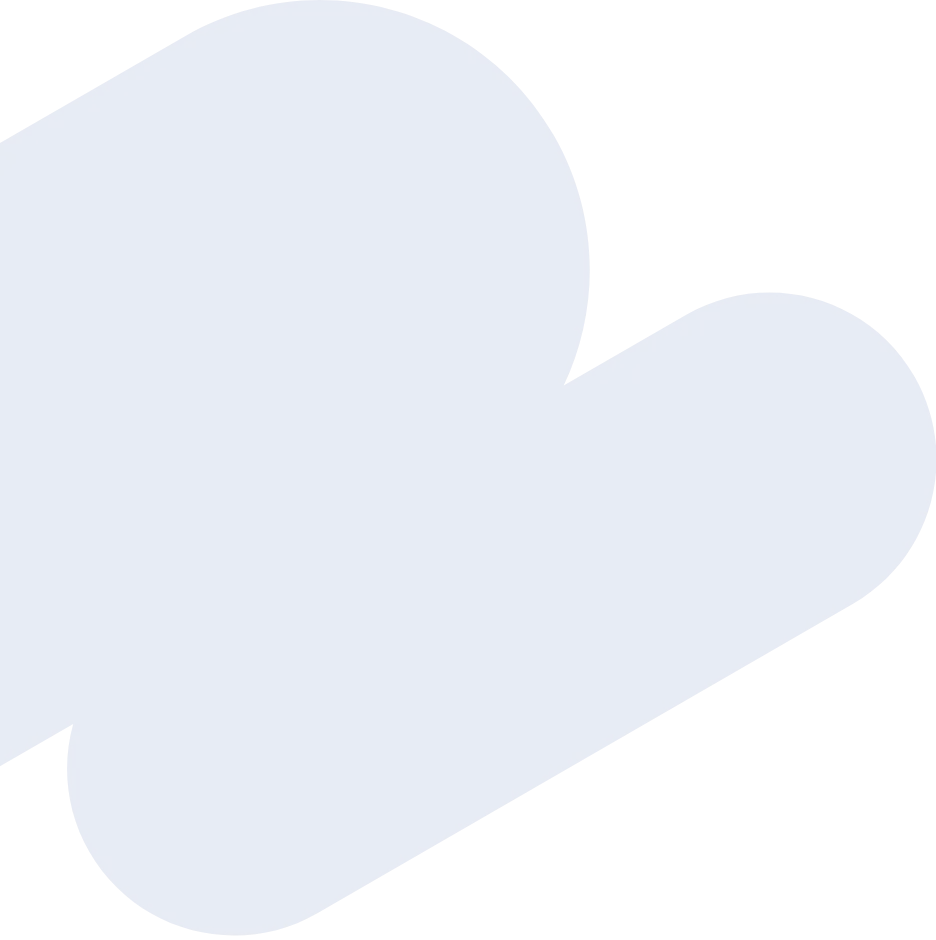
入社3年でビジネススクールへ
成長を後押ししてくれる
社風です
大学で化学を学んでいた私は、入社時は経営についてまったく知識がありませんでした。しかし入社3年後ぐらいに、経営工学を学ぶために会社のサポートのもとでビジネススクールに通い始めました。部長が「行ってこい」と。週に3回程度、16時半に仕事を抜けてスクールで講義を受けるという、よい経験をさせてもらいました。昭和丸筒は、ものづくりはもちろんのこと、人づくりをとても大切にする風土があり、社員の学びや成長を応援してくれます。社内外での学びを後押ししてくれるので、成長のチャンスは豊富です。
また、100年企業でありながら保守的ではなく、自由な空気があると思います。
新しい価値やイノベーションは既成概念の枠を越えたところから生まれてくるものであり、自由な発想を持って一人ひとりのやりたいことが実現できる環境にあります。そうした積み重ねにより、お客様と社会の期待に応える新しい製品や技術を生み出してきたのだと思います。
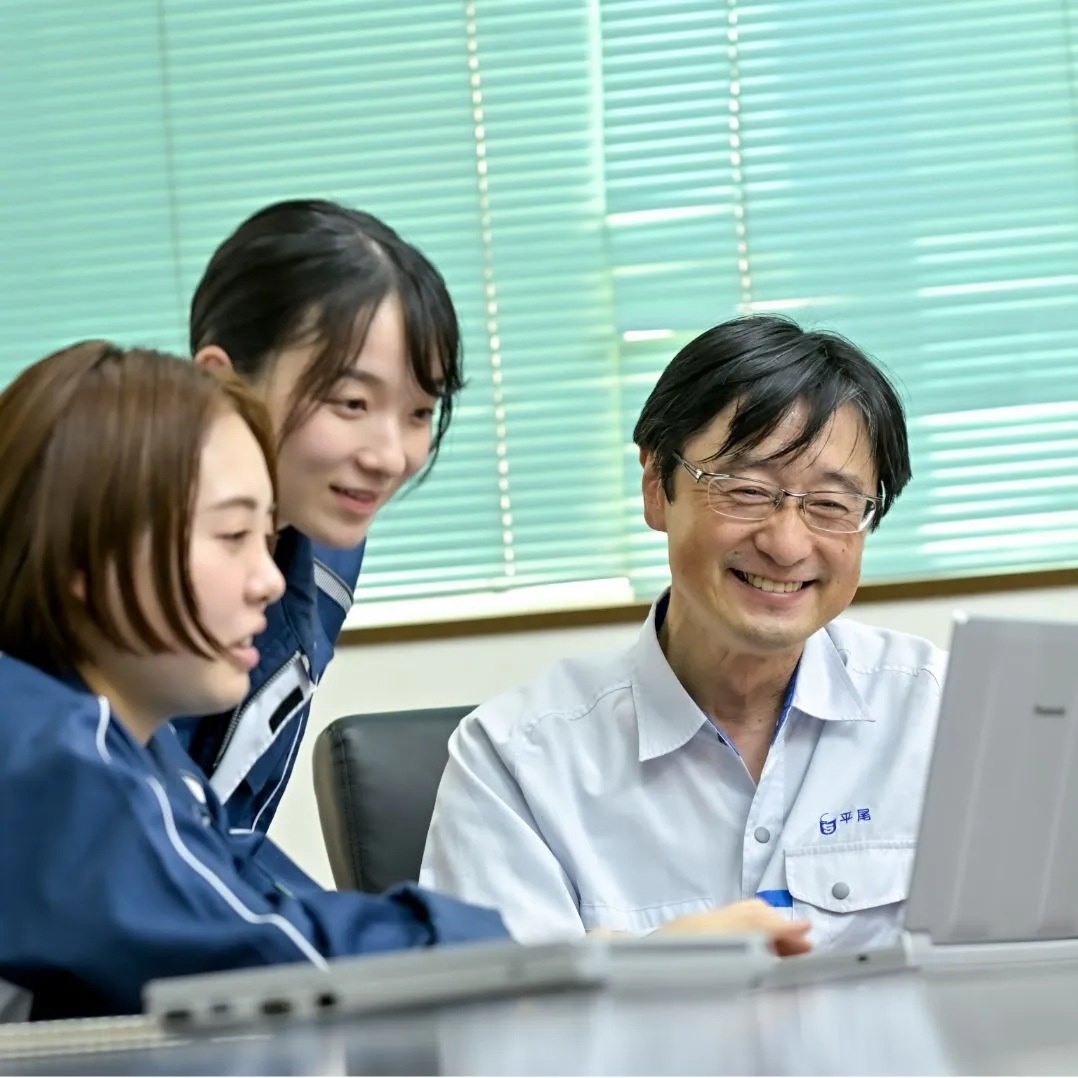
昭和丸筒らしさに注目! FOCUS
100年企業の高い技術力
お客様のニーズにお応えする多種多様な製品を作ることができる技術はもちろんのこと、私たちは製品を作る機械も製造できる技術を持っています。100年にわたり積み上げてきた技術開発の知見、ノウハウは、他社には真似できない100年企業の強みです。
一方、100年間成長できたのは、社会や市場の変化に呼応して、変化と進化を重ねてきたからです。これからも私たちは、若いみなさんと一緒に、よりよい未来に向かって変化し、進化していきたいと思います。
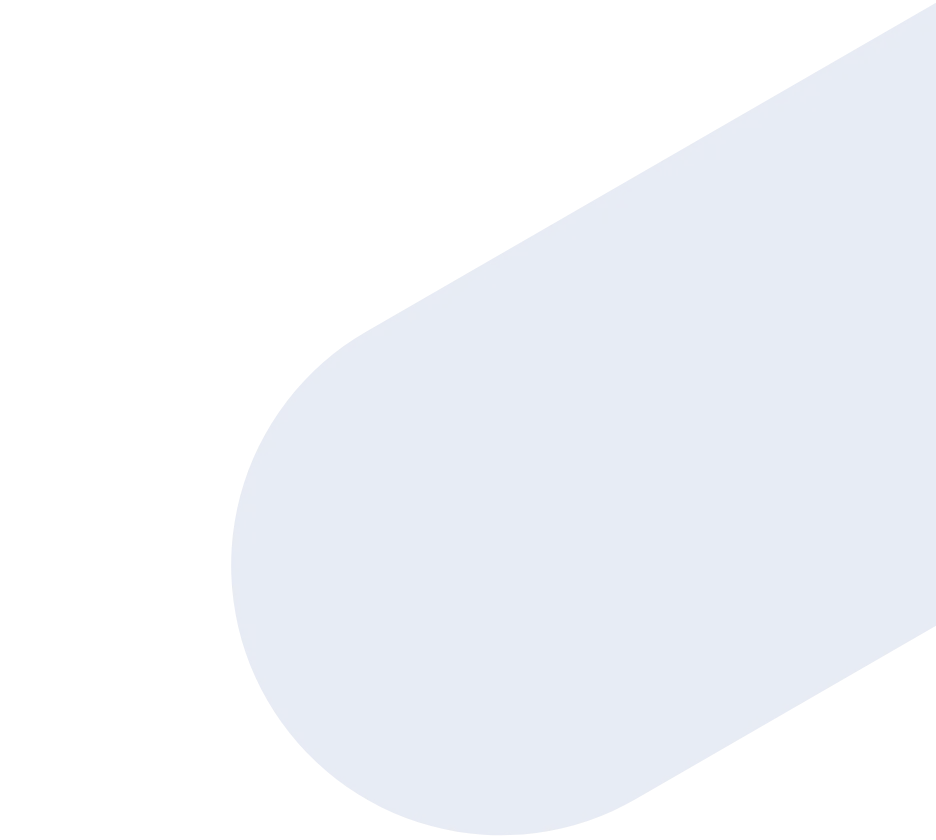
未来の後輩のみなさんへ MESSAGE
ものづくりのデジタル化に向けて
ぜひ力を発揮してください
製造部では、生産活動のデジタル化に力を注いでいます。例えば、紙ではなくモニターを使って工場の実績管理をする。あるいは製造の不良率などの数字をモニターに映して課題を見える化し、現場で共有して改善につなげていく。また、製造個数をタッチパネルで入力できるようにすることで、業務の効率化を図る、といった取り組みを進めていきます。
こうしたものづくりのデジタル化に興味のある人と、ぜひ一緒に仕事をしたいです。
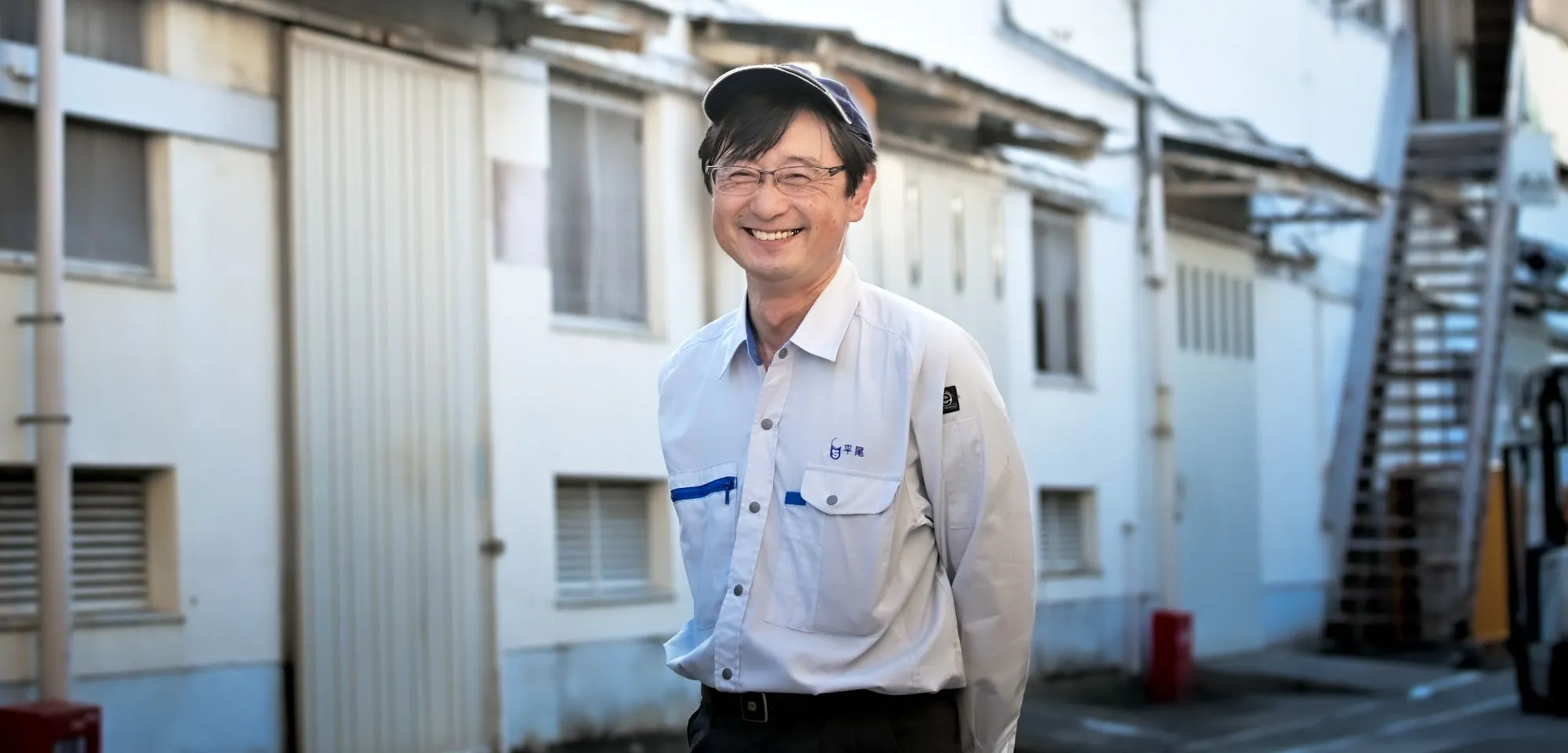